Materialforschung
Abheben mit Hightech
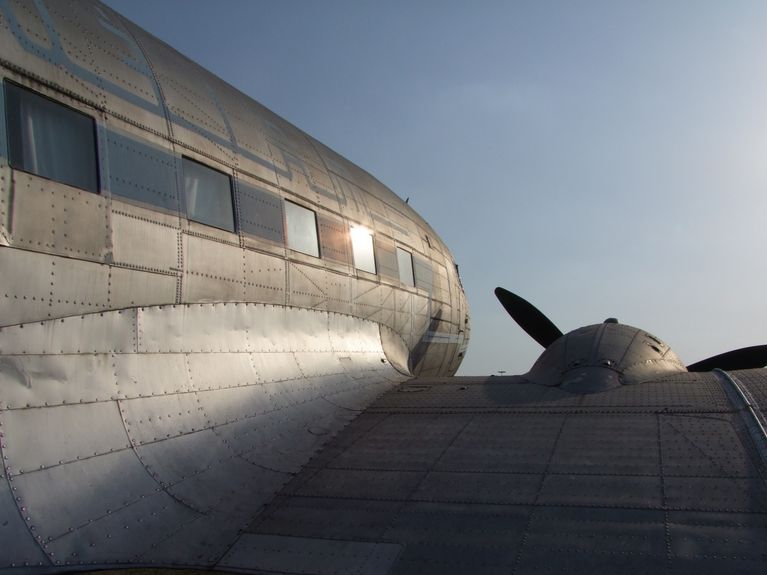
Bild: fotolia.com
Leichter sollen sie werden, sparsamer - und natürlich sicherer: Flugzeuge sind für Materialforscher eine echte Herausforderung. Wissenschaftler in Geesthacht arbeiten an einem Verfahren,das für den Jet von morgen richtungsweisend sein könnte
Unfreiwillig luftig: Risse an Nietenreihen sorgten dafür, dass dieser Flieger 1988 sein Dach verlor. Bild: picture alliance / AP Photo / Robert Nichols
Es war der 28. April 1988, der den Blick auf den Flugzeugbau grundlegend verändert hat: In mehr als 7.000 Metern Höhe löste sich bei einer Boeing 737-200 der Aloha Airlines ein großes Stück des oberen Rumpfes - nur mit Mühe konnte der Pilot den Jet noch notlanden, der urplötzlich zum Cabrio geworden war. Der Grund für das Unglück mit einer Toten und 65 Verletzten: Zwischen zwei Nieten-Reihen in der Flugzeughaut hatte sich ein Riss gebildet.
"Wenn man Flugzeuge ohne Nieten bauen kann, ist so ein Fall praktisch ausgeschlossen", sagt Norbert Huber, Leiter des Instituts für Werkstoffforschung am Helmholtz-Zentrum Geesthacht. Mit seinen Kollegen arbeitet er an innovativen Methoden, um die verschiedenen Komponenten von Flugzeugrümpfen zusammenzufügen. Sicherheit ist dabei ein wichtiger Faktor - genauso wie die Suche nach Gewichtseinsparungen, die das Fliegen in Zukunft deutlich umweltfreundlicher machen sollen.
Wie wichtig die Forschung ist, zeigt ein Blick auf die Statistik: Jedes Jahr wächst die kommerzielle Luftfahrt weltweit um rund fünf Prozent. Airbus schätzt den Bedarf an neuen Flugzeugen in den kommenden 20 Jahren auf rund 30.000 Jets, eine gigantische Zahl. Die große Revolution im Kampf gegen die Kilos bei der Konstruktionsweise steht dabei gerade am Anfang. Boeing baut seinen Zweistrahler 787, der schon im Einsatz ist, überwiegend aus Kohlefaser-Verbundwerkstoffen (CFK). Der neue Airbus A350, der ab Ende 2014 im Liniendienst fliegen soll, wird ebenfalls aus dem leichteren Material gebaut. Diese Flugzeuge sparen wegen der neuen Bauweise etwa ein Fünftel der bisherigen Betriebskosten, versprechen die Hersteller. Lukrativ ist das vor allem bei großen Flugzeugen. Aber: "Rund 80 Prozent der in den nächsten 20 Jahren gebauten Jets werden zu den kleineren Typen mit nur einem Mittelgang ("single-aisle") gehören. Nach heutigen Überlegungen sollen diese Flugzeuge weiterhin aus Metall gebaut werden", sagt Jorge dos Santos, Materialwissenschaftler in Geesthacht. "Das ist bei CFK vor allem eine Kostenfrage beim Material und bei der Herstellung, außerdem ist durch das bisher ungelöste Recycling-Problem bei CFK die gesamte CO2-Bilanz ungünstig." Dos Santos arbeitet daran, Metall für den Flugzeugbau der Zukunft attraktiver zu machen - und zwar durch verbesserte Fügetechnik.
Bis heute nämlich bestehen Flugzeugrümpfe zumeist aus hochfesten Aluminiumblechen, deren einzelne Hautfelder durch Nieten miteinander verbunden werden. Rund eine halbe Million davon steckten in einem Airbus A310 aus den 1980er Jahren, in einer Boeing 747 sind es rund fünfmal so viele. Die moderne Boeing 787 mit ihrem CFK-Rumpf dagegen braucht nur noch etwa 20 Prozent der Nieten im Vergleich zu einem konventionell aus Metall gefertigten Flugzeug. Das ist ein großer Vorzug, denn Nieten zu verarbeiten ist aufwendig.
Genau in der Spur: Ein Schweißkopf fährt die Naht entlang. Bild: Helmholtz-Zentrum Geestacht/Christian Schmid
"Auf die gesamte Struktur bezogen nimmt das Setzen einer Niete durchschnittlich etwa eine Minute in Anspruch", sagt Norbert Huber. Nieten bringen außerdem eine Menge zusätzliches Gewicht, verschlechtern die Aerodynamik der Flugzeugoberfläche und sind obendrein anfällig für Rissbildung in den eigens ausgebohrten Löchern. Eine Alternative zu den Nieten im Metall-Flugzeugbau, so hat die Arbeit der Geesthachter Forscher ergeben, kann das Schweißen sein. Im kleinen Rahmen wird etwa bei den kleinsten Airbus-Typen A318 und A319 sowie beim Größten, der A380, heute bereits das Laserstrahl-Schweißverfahren genutzt. Bisher allerdings ist die Branche zögerlich. "Die Flugzeughersteller müssen wir noch überzeugen, die haben oftmals Bedenken gegenüber dem Fügen, weil durch die entstehende Hitze das Material verändert wird", sagt Jorge dos Santos. Das gilt für die herkömmlichen Schmelz-Schweißverfahren mit hohen Temperaturen von bis zu 700 Grad Celsius. Die Anforderungen an solche Fügetechniken sind extrem hoch: "Sie müssen kostengünstig sein, hochproduktiv, effizient und vor allem den Sicherheitsanforderungen im Flugzeugbau genügen. Eine Schweißnaht muss die ganze Lebensdauer eines Flugzeugs halten", sagt Norbert Huber.
Die Helmholtz-Forscher in Geesthacht setzen daher auf ein relativ neues Schweißverfahren, das erst 1991 patentiert wurde und seit Mitte der neunziger Jahre etwa im Raketen- und Schiffbau Anwendung findet: das Rührreibschweißen. "Hier wird mit wesentlich niedrigeren Temperaturen von um die 400 Grad Celsius gearbeitet. Dabei wird nichts geschmolzen, sondern das Material wird zunächst durch Reibungswärme teigig gemacht und dann miteinander vermischt", erklärt dos Santos. "Es wird durch die Rotation eines mechanischen Werkzeugs in Scherströmungen versetzt, wie ein im Becher umgerührter Joghurt", ergänzt Norbert Huber, von Haus aus Werkstoffmechaniker. "Nach dem Abkühlen bildet das Material eine neue und sehr viel feinere Mikrostruktur, die sehr gute mechanische Eigenschaften hat. Ein möglicher Qualitätsverlust bei der Erwärmung wird durch die feinere Mikrostruktur teilweise wieder wettgemacht."
Schweiß-Experten: Jorge dos Santos (links) und Norbert Huber vor der Robotik-Portalanlage
Die Vorteile des Rührreibschweißens für den Flugzeugbau sind vielfältig: "Es ist ein robustes Verfahren, das nicht auf kleine Fertigungsabweichungen reagiert und sich daher sehr gut als Produktionsverfahren eignet", sagt Jorge dos Santos. Und es ist heute schon um die Hälfte schneller als das Setzen von Nieten, "anderthalb Meter pro Minute schaffen wir jetzt", erklärt der Materialwissenschaftler. Außerdem leichter - im Vergleich zu einer genieteten Konstruktion wird ein halbes Kilogramm pro Meter Schweißnaht eingespart. Die Lebensdauer der Flugzeugstruktur verlängert es ebenfalls, weil im Gegensatz zu Ermüdungsrissen an Nietlöchern keine Quellen für Rissbildung eingebracht werden - das war die Ursache bei dem Unglücksflug der Aloha Airlines.
Der sechsfache Lebenszyklus eines normalen Flugzeugs ist beim Hersteller Embraer in Brasilien mit Rührreib-geschweißten Teilen bereits simuliert worden, ohne dass Risse entstanden wären. Das neue Verfahren bietet sich nicht nur beim Zusammenfügen von Flugzeug-Hautfeldern an, sondern auch bei den Fensterrahmen in Flugzeugen, die heute stets genietet werden. "Da sparen wir zusätzlich pro Fenster nochmal 200 Gramm Gewicht", sagt Huber.
Am Helmholtz-Zentrum Geesthacht wird nicht nur Grundlagenforschung betrieben, sondern auch die praktische Umsetzbarkeit von Innovationen erprobt. Dazu verfügt das Institut für Werkstoffmechanik über ein eigenes Fügetechnik-Labor. Darin befinden sich zwei Schweißroboter für komplexe 3D-Geometrien und eine sechseinhalb Meter lange Robotik-Portalanlage, mit der die Wissenschaftler die entwickelten Verfahren an Flugzeugschalen für die künftige Generation mittelgroßer Flugzeuge erproben. Hersteller wie Embraer oder der Airbus-Zulieferer Premium Aerotec sind schon lange Partner der Helmholtz-Forscher. "Die eingesetzten Robotik-Anlagen sind Prototypen, die wir in den vergangenen Jahren für rund drei Millionen Euro nach dem neuesten Stand der Forschung eigens für diese Arbeiten aufgebaut haben."
Um die Abläufe beim Rührreibschweißen zu demonstrieren, reicht Jorge dos Santos auch eine einfache Demonstrationsanlage. Er legt zwei je zwei Millimeter dicke Blechstücke übereinander in das Gerät und senkt ein staffelholzgroßes Stahlwerkzeug ab. An dessen Spitze befindet sich zunächst die so genannte Schulter, 13 Millimeter breit, an deren Ende wiederum ein 1,9 Millimeter langer, sechs Millimeter breiter Stift mit einem Gewinde. "Das Werkzeug kostet nur 200 Euro. Damit können wir problemlos 1,2 Kilometer Schweißnaht herstellen", sagt dos Santos und lässt den Stift butterweich genau 1,9 Millimeter tief in das Blech eindringen, während er mit etwa 1.200 Umdrehungen pro Minute rotiert. Nach etwa fünf Sekunden sind Eindringvorgang und Aufheizphase beendet und das Schweißen beginnt, zügig bewegt sich der Stift über das Blech vorwärts. Aus der Nähe ist ein wenig Hitze zu spüren, schon sind beide Werkstücke extrem fest miteinander verbunden. Für einen Schweißvorgang läuft das ganze eher unspektakulär ab, keine hellen Lichtbogen, kein Brandgeruch ist zu bemerken. Und genau damit zeigen die Forscher in Geesthacht, dass sie ihren Zielen immer näher kommen. Bereits jetzt werden Boden-Paneele des neuen Airbus A400M-Militärtransporters per Rührreibschweißen zusammengefügt, in Zukunft soll das Verfahren in großem Stil in die zivile Flugzeugproduktion Einzug halten.
Leser:innenkommentare