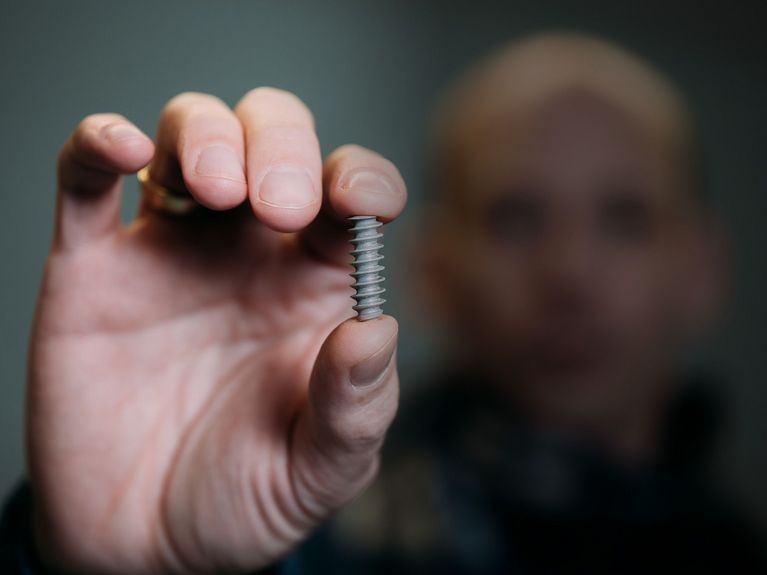
Story #29
Implants That Dissolve in the Body
After a fracture, implants made of titanium or stainless steel are still used to stabilize the bone – and often have to be surgically removed again later. But what if the implants simply dissolved in the body once they were no longer needed? In this regard, Helmholtz-Zentrum Hereon and its partners are exploring the potential of magnesium, and digital twins could help them make breakthroughs.
Often, all it takes is one small mishap to result in broken bones – and implants can be used to help them heal. But conventional metal implants can cause pain and inflammation. Especially in children, whose bones are still growing, they can cause real problems and have to be removed in a second operation after recovery.
Accordingly, for the past 20 years Helmholtz-Zentrum Hereon has pursued research into implants and stents made of magnesium (Mg). As such, it has the expertise needed to tackle the challenging questions involved. The goal: for the material to simply dissolve within the body after three to six months. And magnesium is so bio-compatible that it can even accelerate the healing process.
When it comes to developing Mg implants, both the material composition and processing are essential. At Hereon, two manufacturing chains are being explored: the conventional approach, i.e., alloying, casting, heat treatment, and high-temperature reshaping; and what is referred to as sintering, which is similar to the processes used for firing ceramics. In sintering, the alloy, as a fine powder, is combined with a binding agent to make it malleable and then injected into a mold or 3D printer to form an implant. Once the implant has been made, the next step is to understand the interactions between its material and human tissue. In this regard, Hereon relies e.g. on cellular experiments.
360° Wissenschaft: Die Auflösung - Magnesium für die Medizin [Reupload]
But those interactions are complex. Consequently, digital twins play a critical role in implant development: these virtual models are used to simulate the material’s performance, including its application in patients. The computer models simulate the interplay between the human body and the material, as well as the dissolution and healing process, making it possible to create an individualized Mg implant with the desired dissolution behavior faster and more affordably. To bridge the gap to application, several demonstrators are being tested.
In addition, Hereon is exploring tissue-implant interactions with advanced imaging techniques through its satellite office at the Helmholtz research center DESY. Further cooperation partners include Helmholtz Munich, Karlsruhe Institute of Technology (KIT), and Forschungszentrum Jülich. The Helmholtz Association supports this research e.g. with funds from Helmholtz Imaging (HIP) and the Helmholtz Metadata Collaboration (HMC).
Since 2024, digital implant development has also been intensively pursued in the Cooperation for Digital Implant Research (IDIR), which brings together Hereon, Kiel University (CAU), and the University Medical Center Schleswig-Holstein (UKSH).
Picture: JEWRO Photography
Participating centers
The Helmholtz-Zentrum Hereon conducts international cutting-edge research for a changing world: approximately 1,100 employees generate knowledge and innovation toward more resilience and sustainability. The scientific spectrum encompasses high-performance materials, processes and environmentally friendly technologies for mobility and new energy systems. Furthermore, research is conducted on biomaterials in medicine and for increasing quality of life. Through research and consulting, the Hereon addresses the challenges of climate change in a solution-oriented manner and facilitates sustainable management as well as the protection of the coasts and marine environment through comprehensive scientific understanding.